Dreumex Inside: Exclusive Look into the Production Processes
Jan, can you briefly introduce yourself?
My name is Jan Nauta and I am the production and logistics manager within Dreumex Oss.
Those are quite some responsibilities. What kind of jobs did you have in the past?
Before I started working for Dreumex I worked for 3 years at a technical installation agency in the agricultural sector.. Before that, I gained 30 years of experience at one of the largest paper manufacturers in the world.
Those are quite some responsibilities. What kind of jobs did you have in the past?
Before I started working for Dreumex I worked for 3 years at a technical installation agency in the agricultural sector.. Before that, I gained 30 years of experience at one of the largest paper manufacturers in the world.
What made the switch to Dreumex so interesting for you?
The beauty of Dreumex is that we work a lot with process and mechanical technology. One moment you are busy with pumps and pipes and at another moment with gears and conveyor belts. I just really enjoy the variety within Dreumex. Even after a year and a half, I still encounter new challenges.
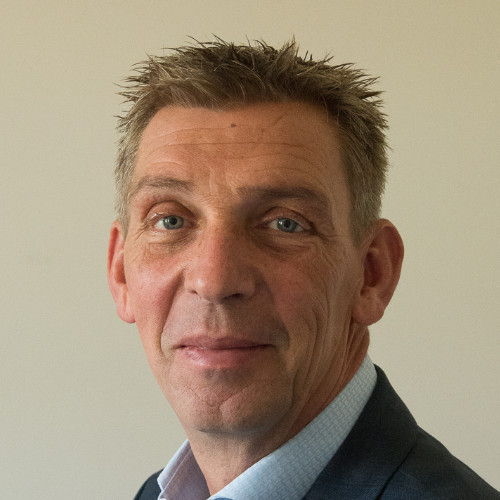
If you look at the time at Dreumex. What are things you look back on with pride?
On the production team and the shown flexibility of the people.
Together with the team, we managed to reduce unnecessary logistical handling. As a result, we have more time we can dedicate to things that have a more positive impact. I was able to set up a learning program based on plan, do, check and act. This not only created independence but also a higher output. On average, we see 15% higher output compared to previous years.
Congratulations, those are impressive numbers! What impact does COVID-19 have on the production?
Due to the high demand for soap and disinfectants the pressure on the production team is higher than usual. Whereas previously we were often able to control the stock and the efficiency of the lines, now we mainly look at the planning on a detailed level. New orders come in every day and our customers want to have it as soon as possible. The demand for products and the availability of components, such as packaging materials, make it an interesting challenge for purchasing and production.
Does the new way of working have an impact on the activities?
Yes it does! The demand for our products is currently enormous. In order to deal with the situation we have been working with shifted shifts for a number of weeks now. This means that for both the production and mixing lines double occupancy is required. Fortunately, the flexibility of the team allows us to achieve this.
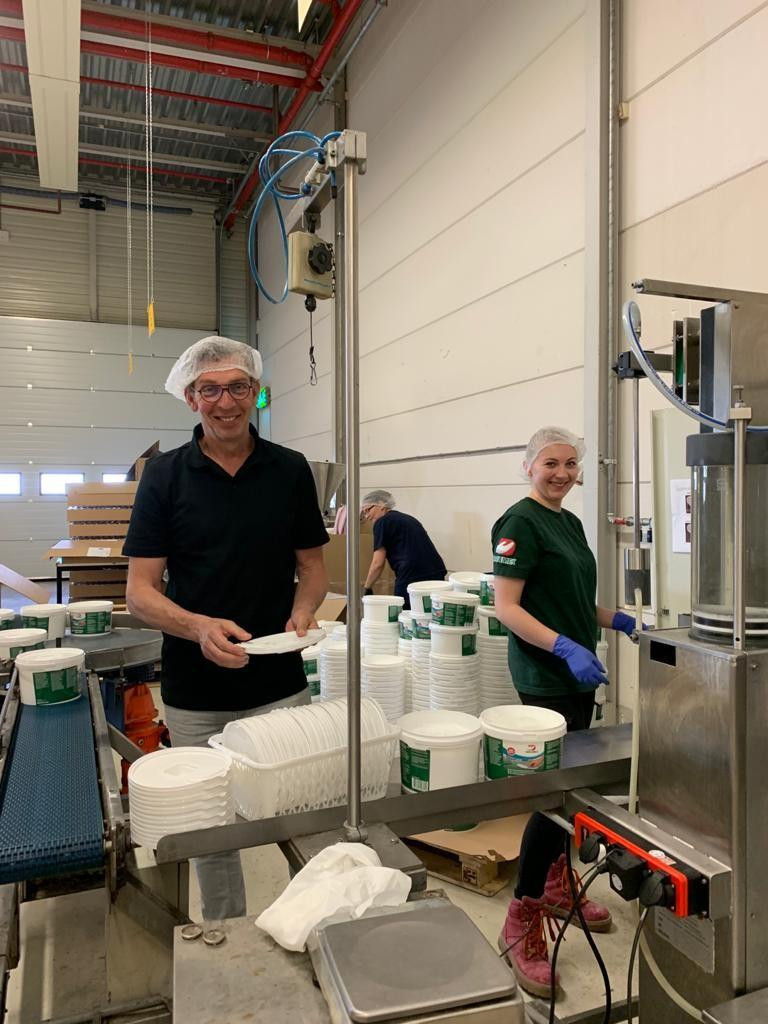
Regarding this new way of working, what kind of feedback did you receive from your team?
It takes some getting used to, but they all understand the importance. In addition to the new way of working, there are also other measures we are taking.
What measures do you take to reduce the spreading risk?
We currently work with a fixed group of people and ensure that everyone follows the RIVM guidelines, including temporary workers. The workplaces are set up in such a way that people can work safely and we ensure that hygienic solutions such as alcohol gel are within reach. In addition, we have shifted breaks and in the canteen everyone is at least 1.5 meters apart.
Furthermore, before the start of the shift every morning I go out on the floor to talk to my team. I think it's important to gauge their health and make sure they're doing well. Especially in these days there has to be extra attention for the people who can't work from home.
That are quite some measures. I assume it also has an impact on the output?Yes, but not as you expect. It actually got better.
As previously stated, due to the virus the demand is now enormous. This ensures that we can show our "production muscles" so to speak. People work hard and the machines run all day long. Overall we see a positive impact on the production numbers.
It sounds like you are achieving impressive results. What kind of support are you receiving from the organization?
It is a bit out of touch if you look at people like dolls who only make products for you. Companies often forget that. A supportive hand or a simple appreciation is enough in most cases. The management of Dreumex tackled this very well by sending an internal video message. The message garnered a lot of positive reactions. This in combination with the necessary treats keeps the motivation up.
Looks like you are handling the situation to the best of your ability. What future challenges do you expect to encounter?
Due to the output we are currently running, the biggest challenge will be the available raw materials. We are currently working on solutions with our suppliers. In all likelihood, everything can continue to run normally, but it requires creative solutions from the entire supply chain.
Interesting look Jan. Thanks for the inside look. Is there anything else you want to share with everyone?
Especially in these times it is important that attention is paid to the person. A few well-meaning questions have more impact than some people realize. Watch yourself and each other.
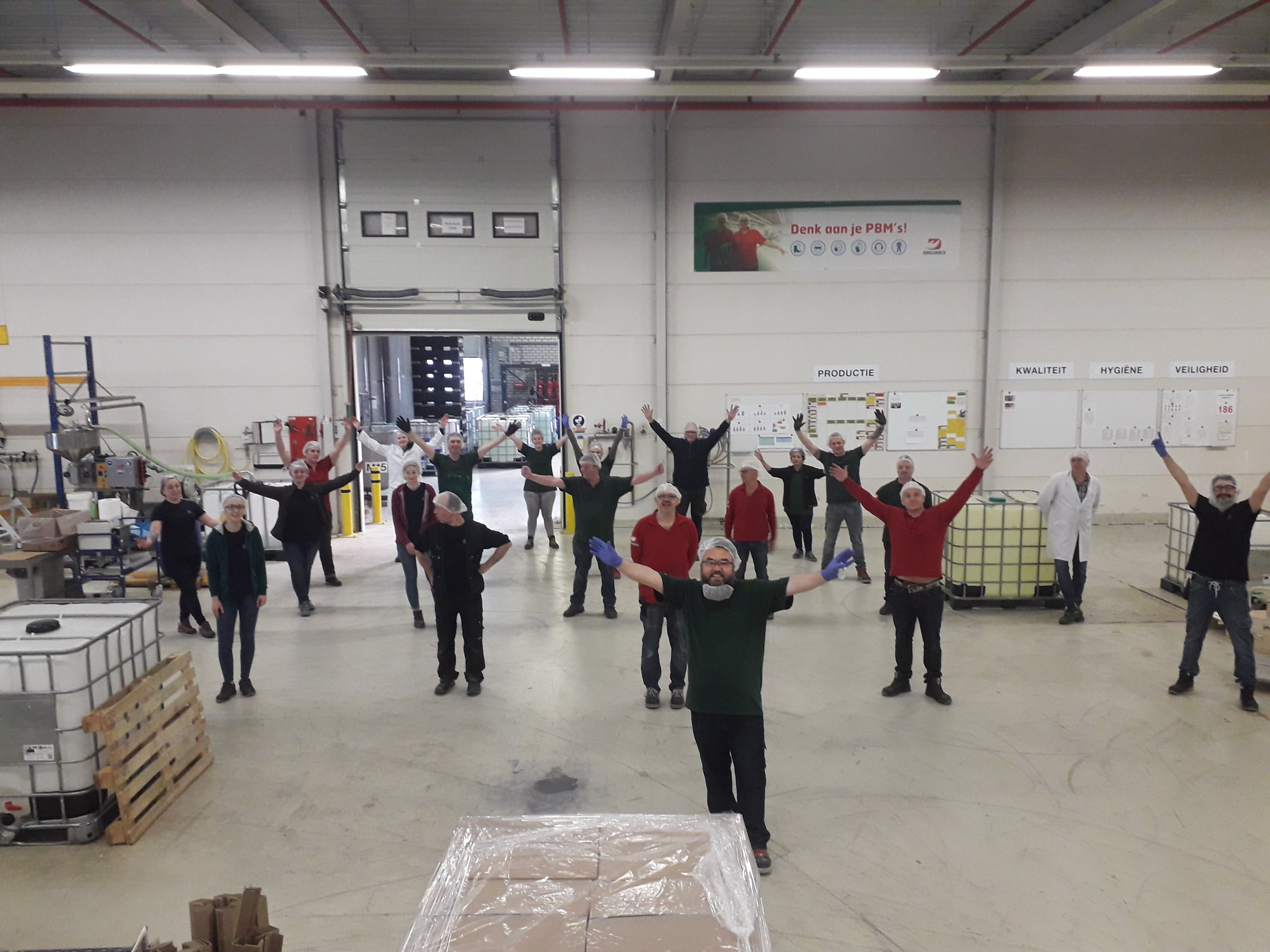